Pellet snack line
_______________
The pellet snacks market has opened up tremendously over the past few years. Consumers are ready to be enticed by flavours, shapes, colours and aromas. Our machines are making pellet snacks in all possible sizes and types.
-
Handling
-
Weighing and dosing
-
Handling
-
Frying
-
Flavouring
Learn more about the Pellet Snack Line
Download brochure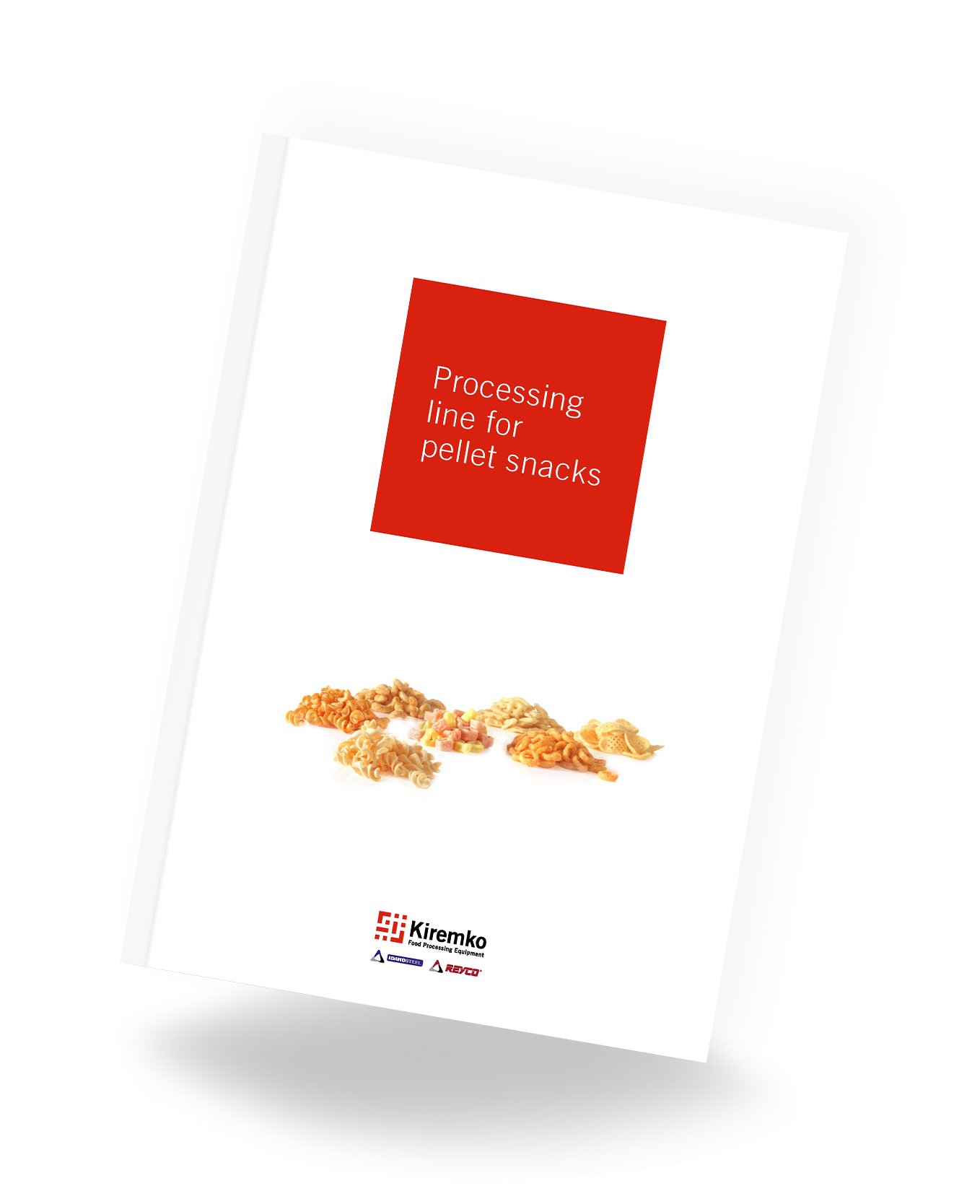
Interested in our product lines
Would you like to know more about Kiremko or our potato processing equipment? Contact us!
Make an appointment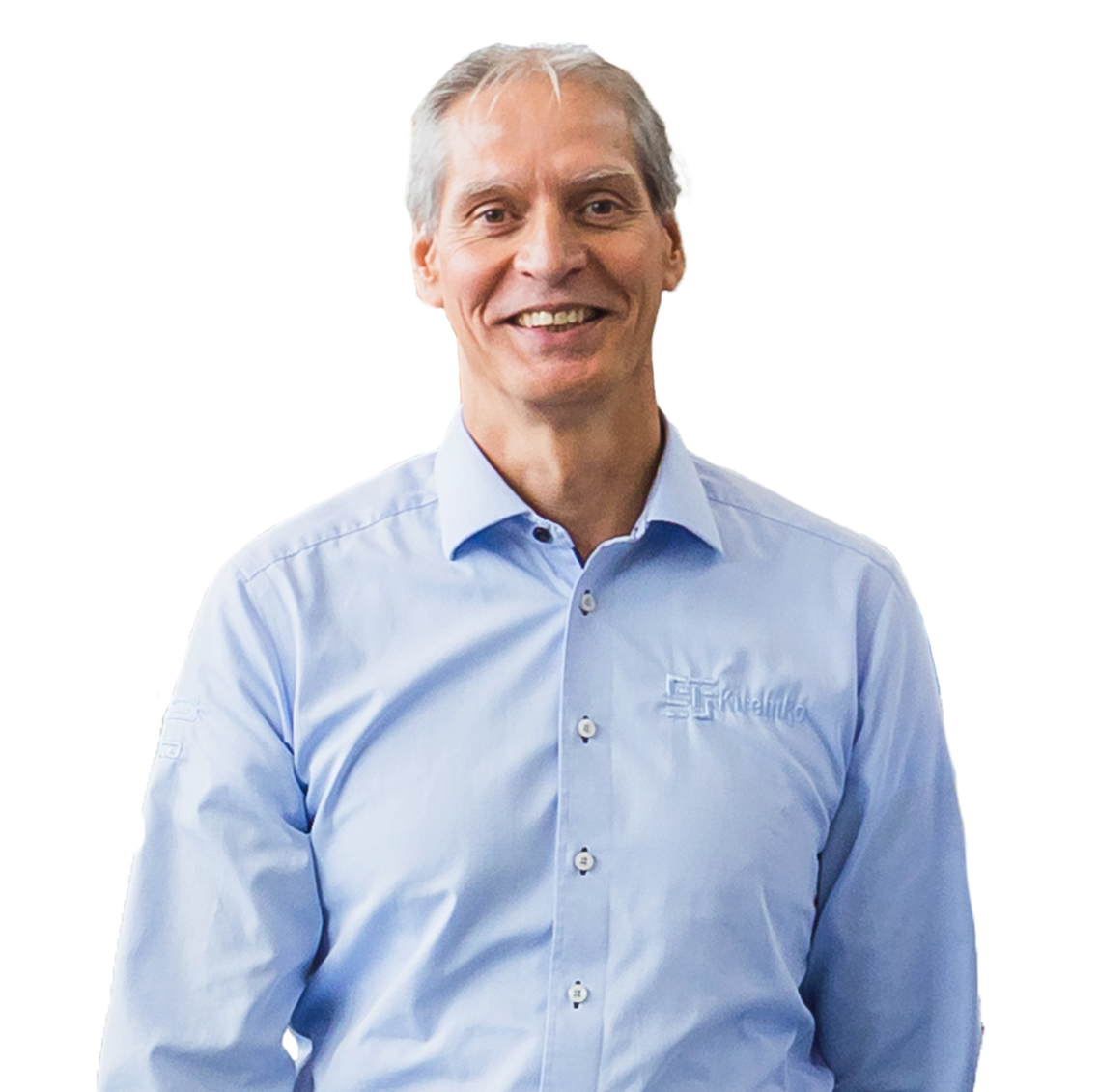
McCrum grows trust
In July 2020 McCrum (Belfast, Maine, US) started up their new Coated French Fries production line with a capacity of 8 tons finished product an hour. The company, founded in 1886, has a rich history of adding value to the potato, from field to plate.
Go to case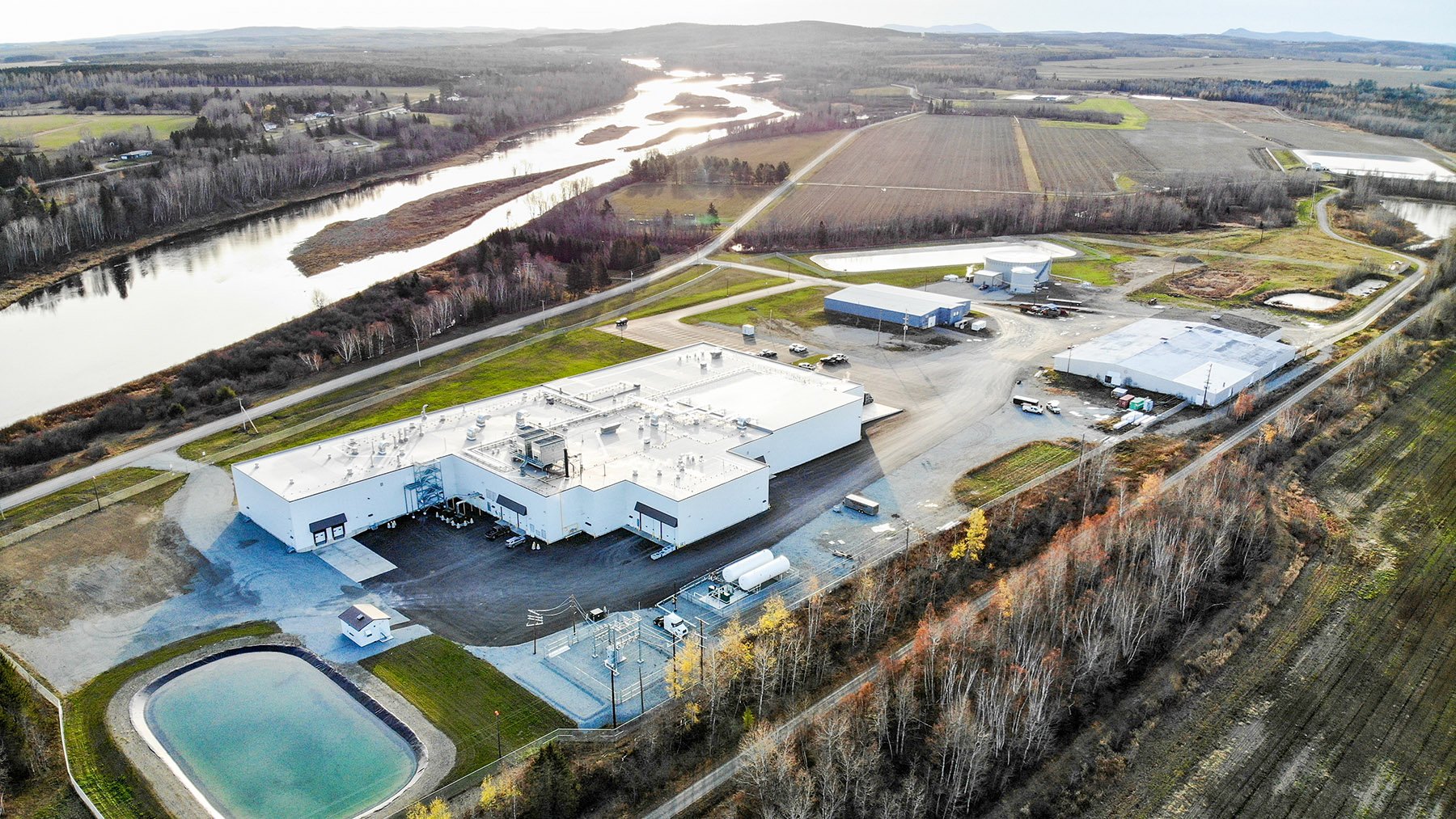