The “Go to Guys” for
Efficient Flake Production
Kiremko
- Keywords
- Idaho Steel
- Drum dryer
- French fry line
- Sustainable
- Mega drum
Ideal solution for sustainability improvement
Because potato byproduct from, for example, the French fry line – think of “slivers” and “nubbins” – can be processed with a production line for flakes into an end product with value.
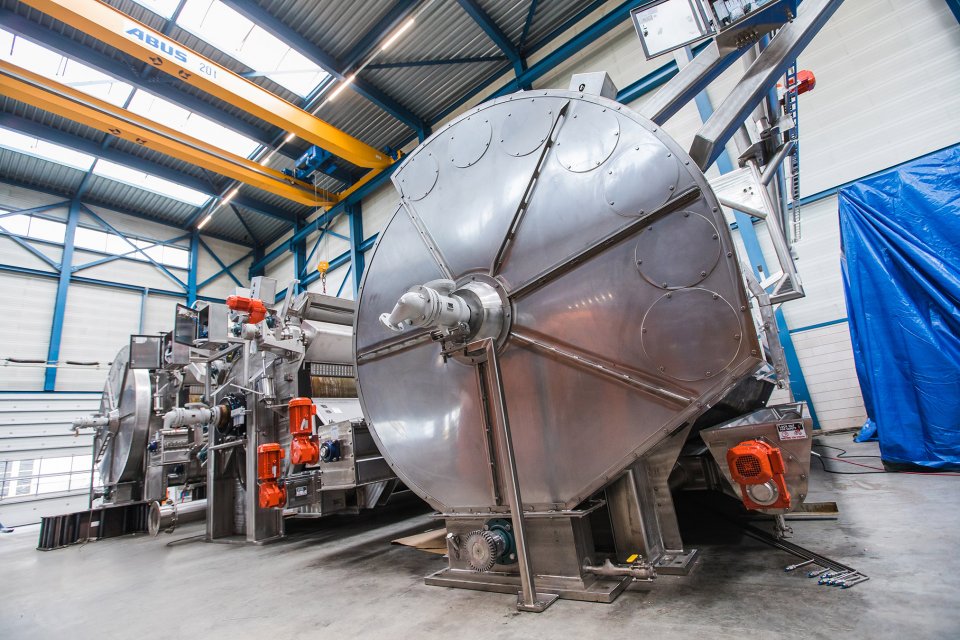
More than 100 years and
250 drums of experience
Kiremko and Idaho Steel, as strategic partners, have now placed more than 200 “drum dryers” around the world. These drums are the heart of the flake line, a heated round “drum” on which the mash potato is dried. With this rich experience, Idaho Steel and Kiremko are able to offer the most effective and high-capacity flake process in the world.
EXCEEDED EXPECTATIONS
In recent years, Idaho Steel and Kiremko have installed a large project in Germany. A flake process line with four drums, good for a requested capacity of 4000 kg per hour. It was agreed with the client that a bonus would be provided if the production line was structurally able to exceed this requested capacity. It is now clear that, after the first 6 months of production, the requested capacity is being exceeded. With more than 20%! The line has been optimally adjusted so that the average steam consumption has decreased significantly. Unfortunately, the figures may not be made public.
NICE ADDITION
Recently, the strategic partners have also delivered two flake projects in Belgium. In both cases, it concerns French fry producers who have had the flake lines installed as a welcome addition to their product range. The Corona crisis in particular made their choice explainable: The potato price fell to an unprecedented level, while the freezer rooms were full. Solution? Making flakes. Idaho Steel and Kiremko were able to respond energetically. Both flake drums were installed within nine months. They are now running at full speed.
MARKET LEADER OF THE CENTURY
Idaho Steel has been around for over a century. In those years they have built up an impressive portfolio on flake drums. More than 200 drums have now been installed worldwide. But an important development has been set in motion for a number of years. The new drums have been built in a new way. The major advantages of this are better heat conduction, (as a result) lower steam consumption and a larger efficient surface. All new factors contribute to a higher return and a better end product. What started all those years ago as “an addition to the range” has grown into an absolute specialty, resulting in worldwide market leadership.
THE “GO TO GUYS” IN IDAHO
Davis Christensen, director of Idaho Steel puts it this way: “In North America, we’ve been the go-to guys when you want to produce flakes since the second half of the last century. And that market has grown enormously since then. Firstly, because you make a potato product with flakes that exceeds the shelf life of other potato products. Second, because potato flakes are used in more and more products, such as instant mash, crisps, flour, snacks and all kinds of binding agent applications. The world of “convenience” in the kitchen, the easy-to-prepare meals, all these developments have contributed to the growth of flake production.
Zero waste as
a starting point
Idaho Steel and Kiremko supply a complete range of potato product lines. From fries to hash browns and from fresh products to flakes. This offer provides for potato processing where raw material loss is kept to a minimum. Potato producers are less and less satisfied with waste that can ultimately only be processed into animal feed biogas or fertilizer. Everything from the potato must be used. Together, Idaho Steel and Kiremko are not only able to offer a solution for all product groups, but above all, find an integrated solution for the zero-waste challenge that producers want to approach.
AN IMPRESSIVE SIGHT
Anyone who has ever stood next to a modern flake drum cannot help but be impressed. Kiremko’s project manager Sander Hoek has a say in this: “Yes, that first time is impressive. But you also get used to it. I have been involved in the installation of six drum dryers over the years. And despite getting used to it, I still think it is great to see that such a large machine can produce such a delicate product. It really is a profession in its own right, in which a versatile flow of raw material – off cuts, potatoes that are too small, etc. – must lead to one consistent end product. It’s great that we master that process like no other.”
TOTAL COST OF OWNERSHIP
The high effectiveness of Kiremko and Idaho Steel drum dryers allows customers to benefit from a low total cost of purchase, operation and maintenance. The construction of the drum dryers is aimed to have the lowest possible steam consumption. Hygiene and safety also played an important role in the development of the machines. The production line in front of the drum dryers is also included in this. Everything is based on optimal economy and ergonomics. The controls of the drum and the “front line” are linked to each other, so that the interplay of cooking, cooling and mashing is precisely tuned to the optimal “load” of the drum.
DON’T BOAST WITH KILOS PER HOUR
Idaho Steel introduced the first stainless steel drum dryer in 1993 and a super drum dryer in 1995. This hygienic machine was an instant hit and the market responded positively. Larger more productive drums followed in the following decades, with increasing global demand. The latest megadrum, produced by Idaho Steel, has a guaranteed capacity of 1,250 kg per hour and can – depending on the dry matter content of the potatoes used – even deliver up to 1,500 kg per hour. “But we don’t use that as a sales argument, because in practice we often have to work with potatoes with a sub-optimal dry matter content. We also do not have to boast with those numbers, because the effectiveness of our drum dryers is also proven by the steam consumption.”
PRIDE DUE
Both partners Idaho Steel and Kiremko are now installing flake lines all over the world. The United States, South America, Europe, Australia, Asia. “And we are currently processing an application for Africa. Then we will have all continents complete again. Because we don’t count Antarctica, no potatoes grow there,” says Kiremko director Marcel van Huissteden with a smile. “Our unique collaboration enables us to make customers all over the world successful in producing flakes. We have been successfully joining forces for almost 25 years, which has meanwhile yielded us a convincing market share and we are proud of that. ”
FLAKES AS INSURANCE
And he continues, saying that recent projects show the great interest in our drum dryers, partly as a result of the global Covid crisis. But flake production will become an indispensable part of versatile potato processing after the pandemic. This is obvious for the specialists, but it may be new for the French fry producers. A flake line as an “insurance policy” for difficult times. So that no potatoes are lost, or to respond more flexibly to the market price of the raw material. Finally, the sustainability assessment will also play an increasingly important role, the zero-waste idea is also permanent. In short, the production of potato flakes is a business case that will stand the test of time.
sustainability improvement
Flake production is not only a potato process for specialists. More and more potato processors see it as an ideal solution for their sustainability improvement. Because potato byproduct from, for example, the French fry line – think of “slivers” and “nubbins” – can be processed with a production line for flakes into an end product with value.
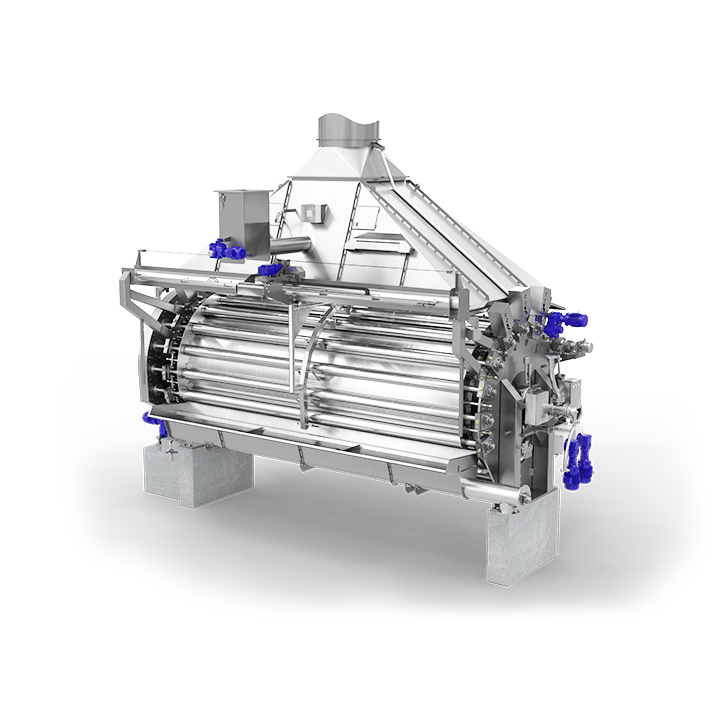
Drum dryers are used to dry cooked potatoes until flakes form. Through cooperation with our partner Idaho Steel, we’ve developed drum dryers with capacities of up to 1200kg/hr. This is 25% more than our competitors, allowing you to make the most of potato by-product.
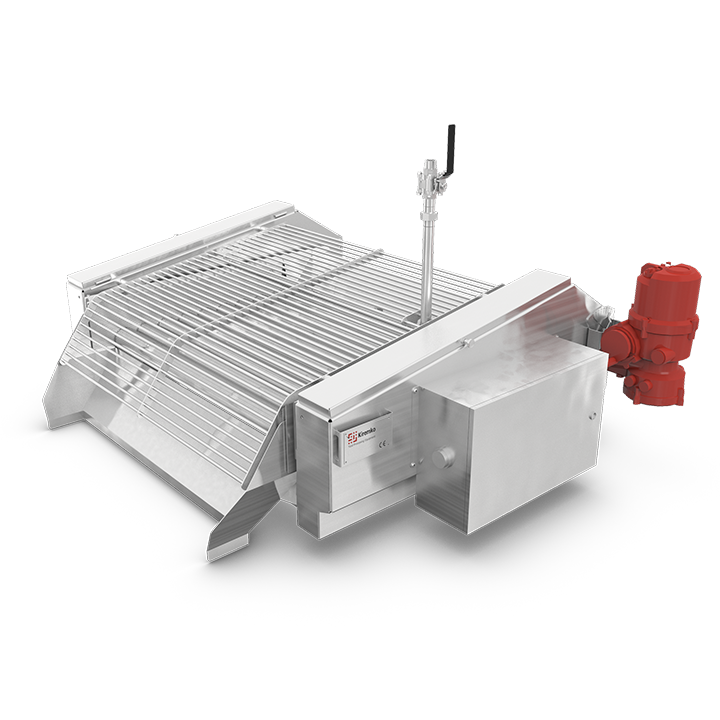
This sliver remover will remove as much as 98% of the cutting residue on your product.
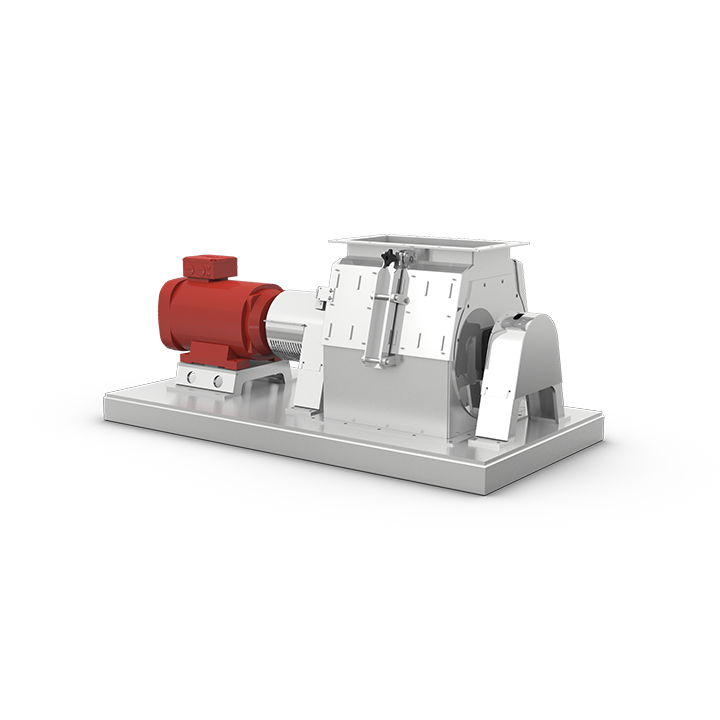
Milling is the final step in the flake process. The milling machine mills potato flakes into flakes that are as small as 1,6 mm x 1,6 mm and as big as 20 mm x 20 mm.
Interested in our product lines
Would you like to know more about Kiremko or our potato processing equipment? Contact us!
Make an appointment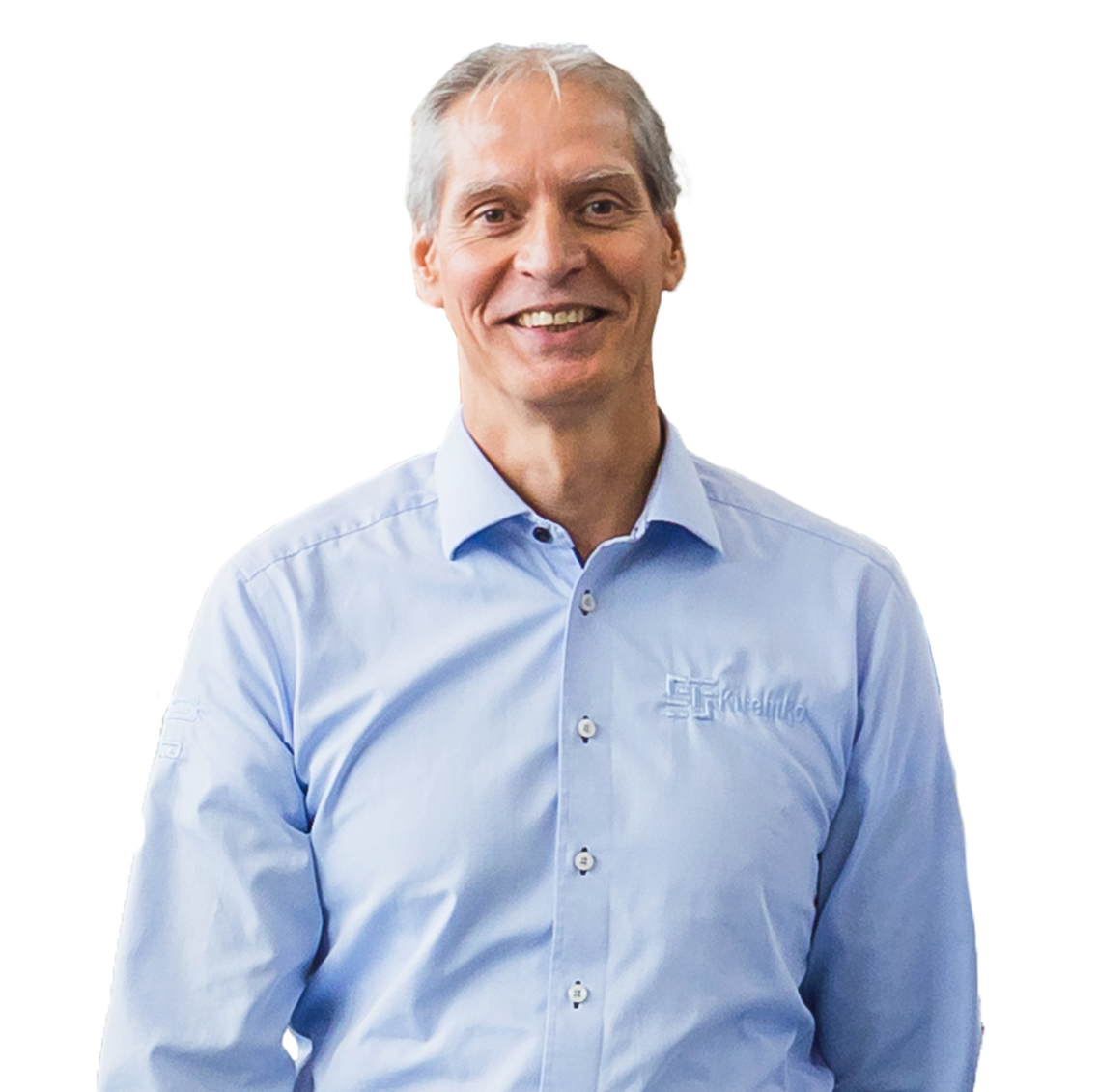